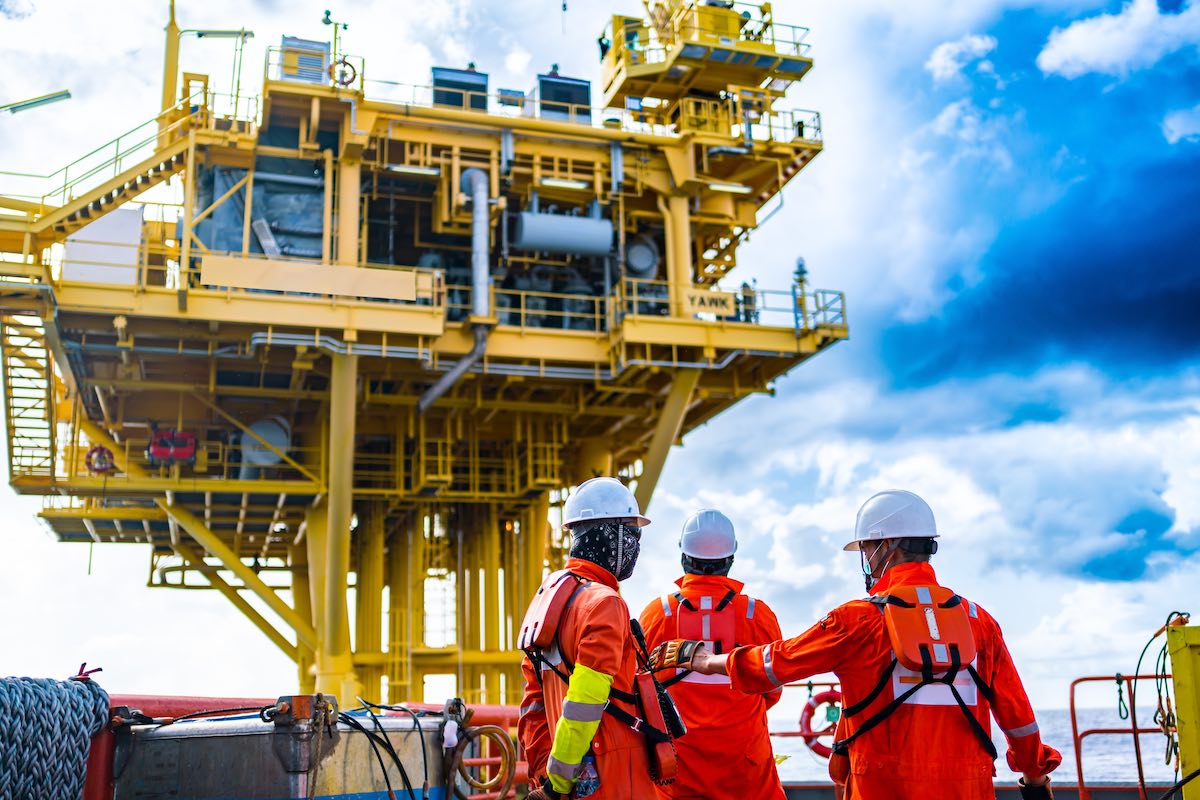
Offshore oil and gas industries are critical to the global economy, extracting and transporting vast amounts of energy resources. However, these industries’ environments are incredibly harsh, with constant exposure to saltwater, chemicals, and fluctuating temperatures. One of the major challenges they face is the risk of corrosion, which can lead to expensive repairs and even safety hazards if left unchecked. This is where spray painting, with specialised protective coatings, comes into play.
Let’s learn how spray painting is used in the offshore oil and gas industries to protect critical infrastructure, extend the service life of assets, and significantly reduce maintenance costs.
The Problem: Corrosion in Offshore Environments
Offshore platforms, pipelines, and oil rigs operate in environments where corrosion is an ever-present threat. The combination of saltwater exposure, chemical processes, and constant UV radiation creates an environment that is extremely conducive to metal degradation.
Corrosion not only weakens the structural integrity of essential assets but also leads to safety hazards and costly repairs. Offshore rigs, in particular, are often far from the shore, making it more challenging to conduct routine maintenance. If corrosion isn’t effectively managed, it could result in catastrophic failures, not to mention production downtime and lost revenue.
Some of the key factors contributing to corrosion in offshore environments include:
Saltwater Exposure: Saltwater is highly corrosive, especially to metal surfaces. When offshore infrastructure like oil rigs and pipelines come into contact with seawater, rust forms rapidly, weakening the metal.
Chemical Exposure: Offshore oil and gas operations often involve the use of corrosive chemicals that accelerate the degradation of metals.
UV Radiation: Prolonged exposure to the sun can cause surface coatings to break down over time, exposing metal to further corrosion.
Given these challenges, it’s clear that a robust solution is needed to protect vital offshore infrastructure from the relentless effects of corrosion.
The Solution: Spray Painting for Protection
Spray painting with specialised protective coatings offers an effective solution for combating corrosion in offshore environments. These coatings create a strong barrier that shields metal surfaces from the harsh elements they’re exposed to, thereby extending the life of the equipment and reducing the need for costly repairs.
Spray painting in offshore industries isn’t just about applying a layer of paint. It’s about using advanced protective coatings designed to withstand the specific challenges of the environment. The key benefits of these coatings include:
Corrosion Resistance: The primary function of these coatings is to prevent moisture, salt, and oxygen from coming into contact with metal surfaces. This prevents rust from forming and slows down the overall process of corrosion.
Chemical Protection: Some spray coatings are designed to resist harsh chemicals that would otherwise degrade metal surfaces. These coatings provide a protective barrier that shields assets from the chemicals used in offshore operations.
UV Stability: Protective coatings are often UV resistant, ensuring they remain durable under constant exposure to sunlight. This prevents the coatings from breaking down and keeps the underlying metal protected.
Types of Protective Coatings Used in Offshore Industries
Different protective coatings are used depending on the specific needs of the offshore infrastructure. These coatings are applied through spray painting techniques for optimal coverage and efficiency. Some of the most commonly used coatings include:
Epoxy Coatings: Known for their excellent resistance to chemicals and water, epoxy coatings are widely used in the offshore oil and gas industries. They are particularly effective in environments where chemical resistance is critical.
Polyurethane Coatings: These coatings are highly resistant to UV radiation, making them ideal for protecting surfaces that are exposed to the sun for extended periods. They also provide a durable finish that is resistant to abrasion.
Zinc-Rich Primers: For steel structures, zinc-rich primers offer excellent corrosion resistance. Zinc acts as a sacrificial metal, meaning it corrodes in place of the steel, thus protecting it from rust. Zinc-rich primers are often used as a base layer, with additional protective coatings applied on top.
Application Process: How Spray Painting Works
The process of spray painting in the offshore oil and gas industries is more complex than simply applying a layer of paint. Proper surface preparation and application techniques are critical to ensuring that the coatings are effective and long-lasting.
1. Surface Preparation: The first step in the spray painting process is to prepare the surface. This involves removing any existing rust, dirt, or debris that could interfere with the adhesion of the coating. Sandblasting or abrasive cleaning is often used to achieve a clean, smooth surface.
2. Priming: In many cases, a primer is applied before the main protective coating. This ensures good adhesion and provides an additional layer of protection. Zinc-rich primers are commonly used for steel structures to enhance corrosion resistance.
3. Application of Protective Coating: The chosen protective coating is then applied using commercial spray painting techniques. Spray painting allows for even coverage across large surfaces, ensuring that all areas are protected. Depending on the type of coating being used, multiple layers may be applied to achieve the desired level of protection.
4. Curing: After the coating is applied, it needs to cure. Curing allows the coating to harden and bond to the surface, ensuring long-lasting durability. Some coatings cure at room temperature, while others may require heat to achieve full hardness.
5. Inspection: Once the coating has cured, the surface is inspected to ensure that the coating has been applied evenly and that there are no areas where the coating is too thin or has been missed.
Cost and Maintenance Benefits
One of the biggest advantages of spray painting with specialised coatings is the long-term cost savings. Offshore oil and gas infrastructure is expensive to build, maintain, and repair. By investing in high-quality protective coatings, operators can significantly extend the life of their assets, reducing the need for frequent maintenance and repairs.
1. Reduced Maintenance Costs: Properly applied protective coatings reduce the frequency of maintenance, as they prevent the build-up of rust and damage from chemicals or UV exposure.
2. Extended Service Life: Spray painting with protective coatings ensures that assets like pipelines, platforms, and oil rigs remain functional for longer periods, reducing the need for early replacements.
3. Fewer Repairs: By preventing corrosion and chemical degradation, these coatings help avoid the need for costly repairs. Offshore operations can continue uninterrupted, reducing downtime and saving money.
Spray painting with specialised protective coatings plays a crucial role in protecting offshore oil and gas infrastructure from the harsh conditions they face. By providing corrosion resistance, chemical protection, and UV stability, these coatings extend the service life of assets, reduce maintenance costs, and help ensure the safety and efficiency of offshore operations.
For offshore operators, investing in high-quality spray-applied protective coatings is essential to maintaining their infrastructure and ensuring smooth operations in the long term.
Protect Your Offshore Assets with APT Spray Painting
APT Spray Painting is a leader in commercial spray painting, offering durable, high-performance protective coatings tailored to the unique needs of the offshore oil and gas industries. Whether you need corrosion protection for pipelines, oil rigs, or other critical infrastructure, APT’s specialised spray painting services ensure long-term durability and reduced maintenance costs.
Visit APT Spray Painting to learn how our expert team can help safeguard your offshore assets.