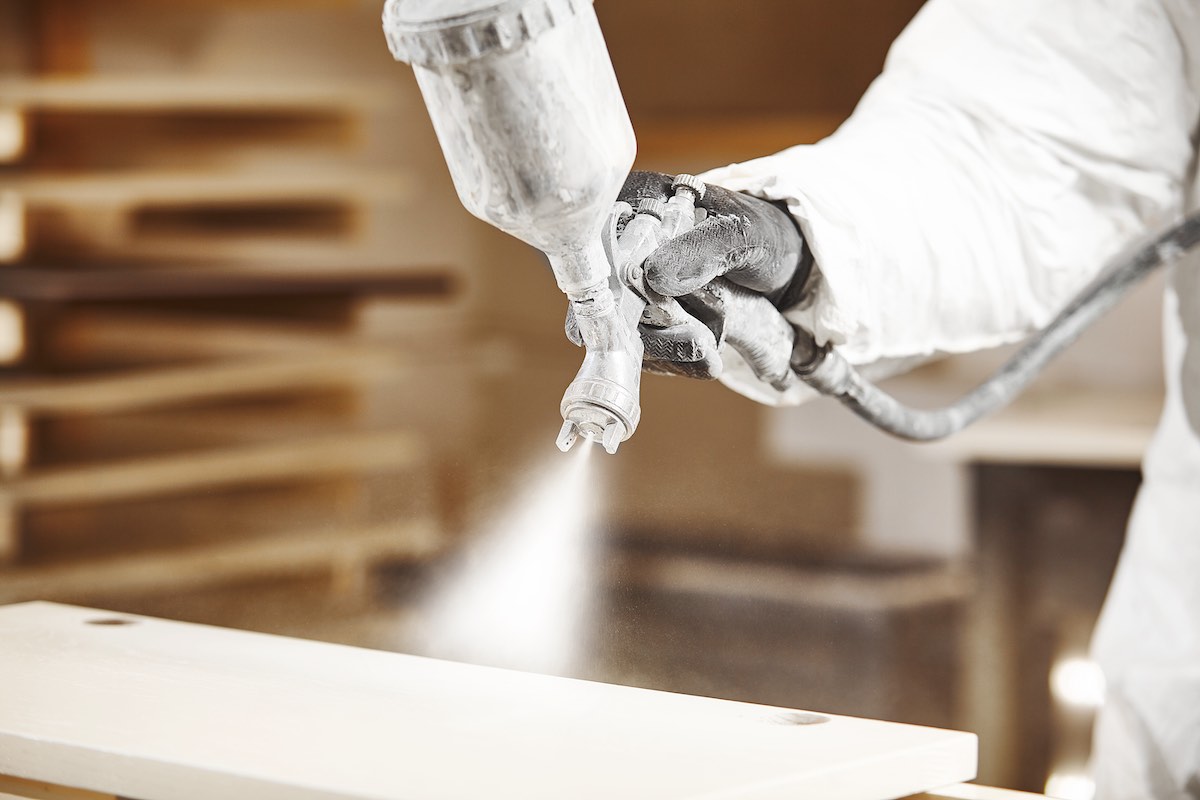
When professional spray painters or manufacturers apply paint or finish to a product, they can use quite a few application methods. Each has its own pros and cons, and some may have multiple variations that fit specific needs. It’s important to consider your budget, goals, and environment when deciding which option is best for you. Here we’ll go over the benefits and drawbacks of the most popular application methods so you can make the best decision on the right choice for your job.
Spray Methods
Spraying is the most common paint and finish application method among industrial manufacturers because it’s versatile and cost-effective. Currently, numerous spray techniques are being used, such as:
Suction – Best For Reliability
A Suction spray gun has a paint reservoir or canister located at the base of the gun. This type of gun has an automatic atomisation process which comes with some beneficial aspects – it provides a smooth, even finish – but can also be a drawback in terms of control over the atomisation, leading to overspray and wasted paint.
Some painters don’t prefer the finish from a Suction fed spray gun, as it lacks control compared to other types of guns. Still, it is a reliable and sturdy piece of equipment that makes up a commercial spray painter’s arsenal.
Airbrush – Best For Details
The airbrush is generally used for more delicate tasks such as coating varnishes, paints, lacquers, shellac and other finishes. This is done by atomising the paint through air and fluid compression, which is known as air spraying.
Airbrushes and spray guns are used for different purposes, but they share one thing in common: both use compressed air to atomise the paint. Generally speaking, spray guns are intended for large-area coverage, while airbrushes are sought after for their precision. However, a variety of hybrids on the market offer a combination of both.
Gravity feed – Best For Smooth Application
Gravity spray guns have become the go-to option for commercial spray painters over the last few decades, ever since they rose to prominence in the 1980s. Compared to siphon-fed paint guns, these gravity fed models require less air pressure, making them more efficient in their paint application.
They also help to reduce overspray, providing greater control and producing a cleaner, crisper finish than other options – making them ideal for detailed tasks.
Pressure Feed – Best For Big Industrial Projects
When it comes to spray units, pressure-fed guns are ideal for tackling large-scale industrial jobs. Instead of sourcing from a pot on the gun itself, these guns extract remotely from a separate pressure pot. This paint sprayer has drawbacks, as it is costlier to run and more complicated to clean; it usually requires extensive flushing out after each colour change.
On the plus side, pressure feed sprayers are strong enough to handle up to 100 litres of paint. They offer advanced control over how the paint is applied via their dual-tank setup – allowing individual fluid and air pressure adjustment. Additionally, they can handle higher viscosity paints than ordinary gravity or suction guns.
Airless
Rather than blending liquid paint with compressed air, airless application machines push the liquid coating through a small opening to generate pressure. This approach shoots paint droplets at a slower speed than regular air-atomised tools, resulting in less waste from over spraying.
Although it does offer several perks compared to standard techniques, airless spraying necessitates further equipment maintenance plus skilful operation by the user. But overall, this method provides excellent results and offers a top-notch finish on any surface. This makes it an ideal choice for large surface areas since coverage is consistent and fast-drying time is achieved quickly.
Electrostatic
Electrostatic applications are a relatively recent development with remarkable transfer efficiency compared to other spray techniques. The equipment charges the paint particles with an intense voltage, attracting them to the part and even wrapping around the contours, allowing for a smooth and solid coat with minimal effort.
This method can dramatically reduce wasted materials but needs skill and precision. Electrostatic equipment handles specialised paints with particular conductivity, so only specific chemical compositions can be used.
While this method can reduce wasted materials significantly, it also requires skill and precision to use safely. Electrostatic equipment is designed for specialised paints that have a specific conductivity, so the options are limited to specific chemical compositions.
APT Spray Painting works across a broad range of industries, providing spray painting solutions that address the functional and aesthetic requirements of any project. If you need a high-end finish for industrial or commercial equipment, we can help. Be sure to get in touch for more information.